Share
Pin
Tweet
Send
Share
Send


Milling cutters of this type are used for a wide variety of materials: wood, ceramics, plastics, various composites and even metal. Their main difference is that the cutting part is small, and is able to process only the end zone of the workpiece, more precisely its contour.
Such processing is designed exclusively for automatic operation from a machine tool or power tool, such as a drill or perforator. Ballerinas are advantageous in that they save energy and time on cutting or milling an exact circle of large diameters. In this article we will tell you how to make such a do-it-yourself milling cutter from improvised materials. So let's get started!
Materials:
- Metal plate 200x25x4-6 mm;
- Bolts: M8 - 2 pcs (+2 nuts and 4 washers); M10 - 1 pc (+2 nuts and 1 washer).
Instruments:
- Drill or stationary drilling machine;
- Bulgarian (angle grinder) with cutting and grinding discs;
- File;
- Screw clamps;
- Drills for metal 9-10.5 mm;
- Core;
- Vise
- Adjustable wrenches and spanners;
- Ruler and marker for marking.
Step-by-step production of a ballerina mill
The base of our cutter is a metal plate. It must be cut to a length of 20 cm.


Mark the center of the plate, screw it up and drill with a 10.5 mm drill. This is best done on a stationary drill press.



Next, mark the middle of the strip, and near its edges we mark the marks for drilling. In order not to break the drill during operation, the interval of core marks should be slightly larger than the diameter of future holes.
We drill holes at the marks on both sides of the plate, not reaching the edges and the central hole literally 1 cm.



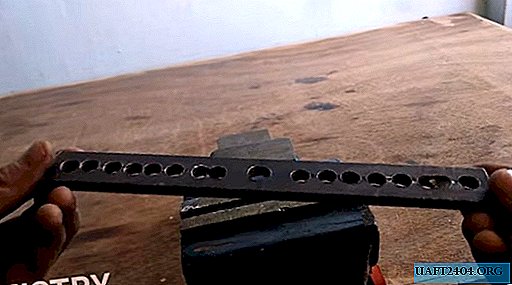
Clamping the plate in a vise, the cutting disc of the grinder connects the holes in two oblong grooves. We finish them with a flat or square file so that future incisors walk in them freely. We also remove mounds and burrs.




We press the plate with clamps to the table or clamp it in a vice. With a grinding disc, we clean its planes, and smooth out sharp corners and edges.


We insert the M10 bolt into the central hole, and tighten it with the nut on the reverse side. We wrap the second locknut over the first and also tighten with an adjustable or open-end wrench.



We make working cutter cutters from M8 bolts. We clamp them in a vise by a hat, glue an unaffected area with masking tape, and use the grinder to engage the threaded part of the bolt. Then we turn the bolt over and grind the opposite part of the bolt, leaving a flat handle 4-5 mm thick. The tips of the incisors are made in the form of a small one-sided hook, pointed at the end.




Insert the cutter bolts into the grooves of the plate in the opposite direction from the cutter rod. We lay them with washers on both sides to increase the area of contact with the plate. The remaining thread on the side of the cutters allows you to tighten the nut and fix these cutting elements with it.


A feature of this milling cutter, the “ballerina,” is to expose both incisors to an equally remote distance from its center. To do this, mark with a ruler a gradation of dimensions on the side of the plate. Marks are applied with a marker up to half a centimeter.
Grinder do notches on the dimensional marks. So they will remain for a long time, and will be easily distinguishable during work.


We set the cutters to the size of the workpiece. Now, holding it in the chuck of a drilling machine, you can accurately and as quickly as possible cut a circle of large diameter, for example, from plywood!



Share
Pin
Tweet
Send
Share
Send