Share
Pin
Tweet
Send
Share
Send

In the mechanisms of previous years of production (machines, gearboxes, drives), gears and gears were often made of gray cast iron, which at low and medium loads were not inferior to steel counterparts, and the casting process was simpler and cheaper than steel.

But cast iron is brittle, and in the gears and gears with a sharp change in load or its increase, the teeth broke, and the whole mechanism failed. Of course, it would be better to replace a gear or gear with a missing tooth with a new product, which is not always possible. Then it remains to try to restore the tooth in another way.

One of the options is related to the mechanical preparation of the place of a broken tooth, surfacing of a material suitable for strength and other characteristics, and the processing of surfacing to obtain a new tooth that is exact in geometry.
Necessary equipment, devices and materials
For work, we need:
- grinder and mini-drill (drill);
- oxygen-acetylene welding torch;
- ticks;
- biomeasure (measuring head);
- lathe;
- sandpaper;
- a shaft with a nut and a tubular stop for the gear block and gear;
- a cutter for forming a profile of the cavity between the teeth;
- axis of a mill with turnkey capture;
- dividing head milling machine;
- measuring tool (vernier caliper, micrometer), etc.
To fill the gap between two adjacent whole teeth in relation to a broken tooth, we need:
- silicon (silicone) bronze rod;
- flux (main part: borax with a small admixture of magnesium);
- fiberglass welding blanket;
- rags, cloth napkins, etc.
The process of restoring a broken tooth
It consists of three stages:
- Site preparation and filling (sealing) of the gap between two adjacent whole teeth with respect to the missing one.
- Making a holder for a gear-cutting mill and an axis for fixing the gear block and gear on the machine during processing.
- The formation of the tooth profile by sampling the deposited material with a special cutter on both sides.
Preparing the soldering point

Since gray cast iron is difficult to machine mechanically, it is almost impossible to do this with a mini drill. It is better and faster to grind a broken tooth using a grinder.

In the end, you can roughen the base with a drill to roughen the base. This will provide a more durable connection of the deposited material with cast iron.
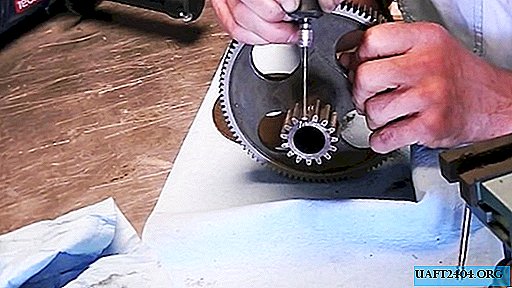

Brazing process

It begins with a thorough and uniform warming up with a gas-acetylene burner, both the soldering place and the adjacent parts of the gear. Otherwise, the likelihood of cracking in the cast iron part increases.
Then the place of soldering and a slightly silicon (silicone) bronze rod are warmed up red, which after heating is lowered into a container with flux, consisting mainly of borax with the addition of a small amount of magnesium.

Next, a silicone bronze rod coated with a flux is placed above the cavity and melted using the flame of a gas-acetylene burner. This operation continues until the siliceous bronze solder fills the entire volume of the cavity between adjacent whole teeth.
At the end of this stage, in order to prevent cracking from fast cooling, we cover the restored part with a fiberglass welding blanket and leave it to cool slowly for the required time.

The process of machining the ends of the gear with soldering

We clamp the gear wheel into the chuck of the lathe and, using the measuring head, set the block with the smallest possible runout, knocking the gear from one side or the other with a mallet if necessary.

Then with the help of cutters we remove the influx of soldering, protruding beyond the ends of the gear. At the end of the grinding with sandpaper, we grind the processing sites.


Preparation of the block and cutters for work

The gear block and gears are mounted on a lathe on a pre-prepared axis by tightening the nut and cylindrical stop.

To make a holder for the milling cutter, we take a steel rod of a certain length and in diameter a little more than the hole in the tool. We clamp it in the chuck of the lathe and from one end we first drill a small hole with a center drill, which we then expand with a spiral drill to the required size.
Next, in the tailstock of the machine, we fix the tap and insert it into the hole on the end of the rod. Take the headstock back and cut the thread by hand, rotating the tap with the knob. In the resulting thread, we screw a homemade bolt with a flat cylindrical head and two symmetrically located rectangular cutouts relative to the center of the rod for gripping with a special key.


Then we end the rod on the other side and drill it to the required length under the diameter of the spindle of the milling machine. Turning is carried out with a periodic check of the diameter so as not to weaken the size. At the end, we grind the turning area with an emery tape and wipe it with a cloth.
Tooth profile formation

We fix the holder of the cutter in the spindle of the milling machine and grind the rod to the size of the hole in the mill, periodically measuring the diameter with a micrometer. At the end, grind the groove with sandpaper and wipe with a rag.
We put the cutter on the holder and fix it on the end with a fixing bolt, first by hand, and at the end with a special key with a screwdriver. Install the dividing head and tailstock on the milling machine desktop. Clamping a perfectly even steel rod between them, we expose these nodes to ensure maximum alignment in the vertical and horizontal planes. To do this, use the measuring heads and adjust the position of the tailstock relative to the dividing head. After exposure, these nodes are securely fastened to the table of the milling machine.
The most important operation is the precise alignment of the cutter with respect to the gear being restored. For this we use a caliper, a micrometer, a metal ruler.


Divide the characteristic of the head by the number of teeth and get the number of revolutions of the handle per 1 tooth. Usually a fractional number is obtained. Then this value is on the circle of the divider.
Now you can turn on the spindle of the milling machine and begin to form one of the cavities of the restored tooth. This is best done in 2-3 passes, so as not to damage the surfacing. When forming a tooth, it is necessary to remove particles of the material being cut from the cutter and lubricate the tool. Next, we retract the cutter and rotate the gear exactly one step with a dividing head and repeat the previous operation again.


One comment
Why take silicon bronze to form a tooth on a cast iron gear? Is it not more reliable to brew a cavity between the teeth with a cast-iron electrode and then process it with a gear-cutter?
If you do this, then due to the high temperature, the cast iron is “bleached” and areas are created that practically cannot be machined. Silicone bronze is similar in strength to gray cast iron, and in tensile strength even higher. Moreover, its processing, as we have seen, is not difficult at all.
Share
Pin
Tweet
Send
Share
Send